APPLICATION STRUTCURE TOPOLOGY
Women Graduates are trained with basics in Industry application from basic science Mathematics, Physics, Chemistry
Training in application Software by Industry Professional, to train others with preparation as TRAINER to empower.
Empowering areas are ACADEMIC SERVICE-ENTREPRENEURSHIP-DESIGN SERVICE-INDUSTRIES-SOCIAL ENGINEERING
AIM of this training is to get employment directly or indirectly from Industries, Government organization either state or central bodies. Also to develop or support rural industries & other application industries either as induvial or self group
Topological optimization
Topological optimization
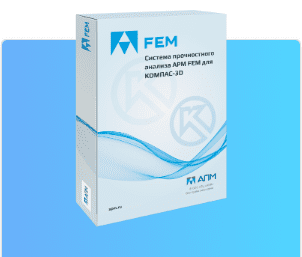
Statement of the problem of topological optimization in APM FEM
To perform topological optimization, it is necessary to determine the objective function and criterion (stiffness maximization, mass minimization), as well as specify the required restrictions (by volume (mass), by stresses, by minimum / maximum wall thickness, symmetry, stamping).
Statement of the problem of topological optimization in APM FEM
To perform topological optimization, it is necessary to determine the objective function and criterion (stiffness maximization, mass minimization), as well as specify the required restrictions (by volume (mass), by stresses, by minimum / maximum wall thickness, symmetry, stamping).
The algorithm for calculating topological optimization is completely identical to any calculation of a conventional model, except for the need to specify the design space as additional initial data (the area where the material can be located under the conditions of design and technological restrictions), as well as special calculation parameters (objective function and criterion, restrictions)
Calculation results and post-processing
As the results of the calculation of topological optimization, the user is presented with a map "Volume fraction" with the possibility of visual removal of "extra" material. The load-bearing frame of the structure obtained in this way must undergo special post-processing in order to obtain a new optimized 3D model, which must go through the verification calculation stage in order to finally confirm its operability. Post-processing is carried out either by specialized KOMPAS-3D tools, or by conventional modeling tools in KOMPAS-3D after export / import of an STL file).
Calculation results and post-processing
As the results of the calculation of topological optimization, the user is presented with a map "Volume fraction" with the possibility of visual removal of "extra" material. The load-bearing frame of the structure obtained in this way must undergo special post-processing in order to obtain a new optimized 3D model, which must go through the verification calculation stage in order to finally confirm its operability. Post-processing is carried out either by specialized KOMPAS-3D tools, or by conventional modeling tools in KOMPAS-3D after export / import of an STL file).
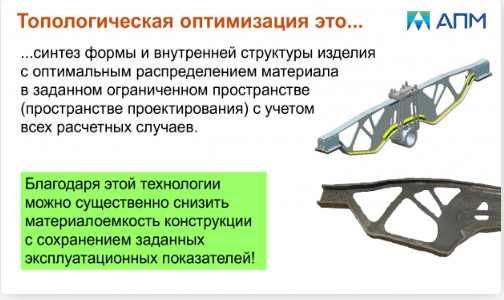
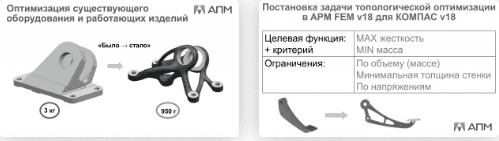
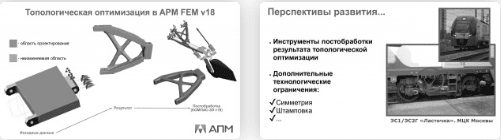