PHYSICS-​APPLICATION SHAFT
Women Graduates are trained with basics in Industry application from basic science Mathematics, Physics, Chemistry
Training in application Software by Industry Professional, to train others with preparation as TRAINER to empower.
Empowering areas are ACADEMIC SERVICE-ENTREPRENEURSHIP-DESIGN SERVICE-INDUSTRIES-SOCIAL ENGINEERING
AIM of this training is to get employment directly or indirectly from Industries, Government organization either state or central bodies. Also to develop or support rural industries & other application industries either as induvial or self group
APM SHAFT AUTOMATIC DESIGN
ANALYSIS-2D DRAWING
Creation of working drawings
With APM Shaft, you can prepare data for further automatic generation of a working drawing of a shaft. The drawing is saved in the APM Graph module in *.agr format.
The final editing of the drawing is done using the APM Graph drawing and graphic editor.
With APM Shaft, you can prepare data for further automatic generation of a working drawing of a shaft. The drawing is saved in the APM Graph module in *.agr format.
The final editing of the drawing is done using the APM Graph drawing and graphic editor.
APM Shaft functionality
With APM Shaft you can calculate and build:
- reactions in shaft bearings;
- diagrams of bending moments and bending angles;
- diagrams of torsion moments and angles of twist;
- deformed state of the shaft;
- stress state under static loading;
- fatigue safety factor;
- diagrams of the distribution of transverse forces;
- eigenfrequencies and eigen shaft shapes.
Calculation results can be saved in an internal file, as well as in a file with *.rtf extension, which can be easily edited if necessary.
APM Shaft functionality
With APM Shaft you can calculate and build:
- reactions in shaft bearings;
- diagrams of bending moments and bending angles;
- diagrams of torsion moments and angles of twist;
- deformed state of the shaft;
- stress state under static loading;
- fatigue safety factor;
- diagrams of the distribution of transverse forces;
- eigenfrequencies and eigen shaft shapes.
Calculation results can be saved in an internal file, as well as in a file with *.rtf extension, which can be easily edited if necessary.
Specialized graphics editor
The APM Shaft module has a specialized graphical editor for defining the geometry of shafts and axes. The editor provides the user with flexible and convenient tools that provide:
- defining the shaft design;
- input of loads acting on the shaft;
- placement of supports on which the shaft is mounted.
A distinctive feature of the graphical shaft editor of the APM Shaft module is the presence of a special set of primitives - these are the main elements of the shaft design (cylindrical and conical sections, chamfers, fillets, grooves, holes, threaded sections, keys, splines, etc.) acting on the shaft loads and supports on which it is placed. The use of such primitives greatly simplifies the input and editing of shaft geometry and other data necessary for performing calculations.
Specialized graphics editor
The APM Shaft module has a specialized graphical editor for defining the geometry of shafts and axes. The editor provides the user with flexible and convenient tools that provide:
- defining the shaft design;
- input of loads acting on the shaft;
- placement of supports on which the shaft is mounted.
A distinctive feature of the graphical shaft editor of the APM Shaft module is the presence of a special set of primitives - these are the main elements of the shaft design (cylindrical and conical sections, chamfers, fillets, grooves, holes, threaded sections, keys, splines, etc.) acting on the shaft loads and supports on which it is placed. The use of such primitives greatly simplifies the input and editing of shaft geometry and other data necessary for performing calculations.
Methods and criteria for calculation
The stressed and deformed states of the shaft are calculated by the methods of resistance of materials. So, the deformed state is described by the Mohr method, and the disclosure of static indeterminacy is performed by the force method. Static strength is evaluated by equivalent stresses obtained by the energy method. Dynamic characteristics such as natural frequencies and natural shapes are determined by the method of initial parameters.
The calculation of fatigue strength is reduced to finding the safety factor in the current section along the length of the shaft, both at a constant external load and in the case when the law of its change with time is known.
Methods and criteria for calculation
The stressed and deformed states of the shaft are calculated by the methods of resistance of materials. So, the deformed state is described by the Mohr method, and the disclosure of static indeterminacy is performed by the force method. Static strength is evaluated by equivalent stresses obtained by the energy method. Dynamic characteristics such as natural frequencies and natural shapes are determined by the method of initial parameters.
The calculation of fatigue strength is reduced to finding the safety factor in the current section along the length of the shaft, both at a constant external load and in the case when the law of its change with time is known.
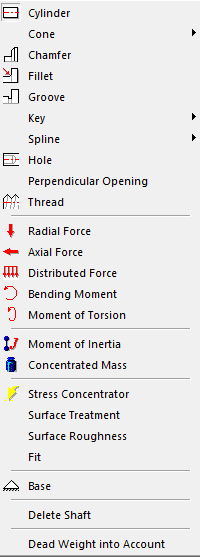
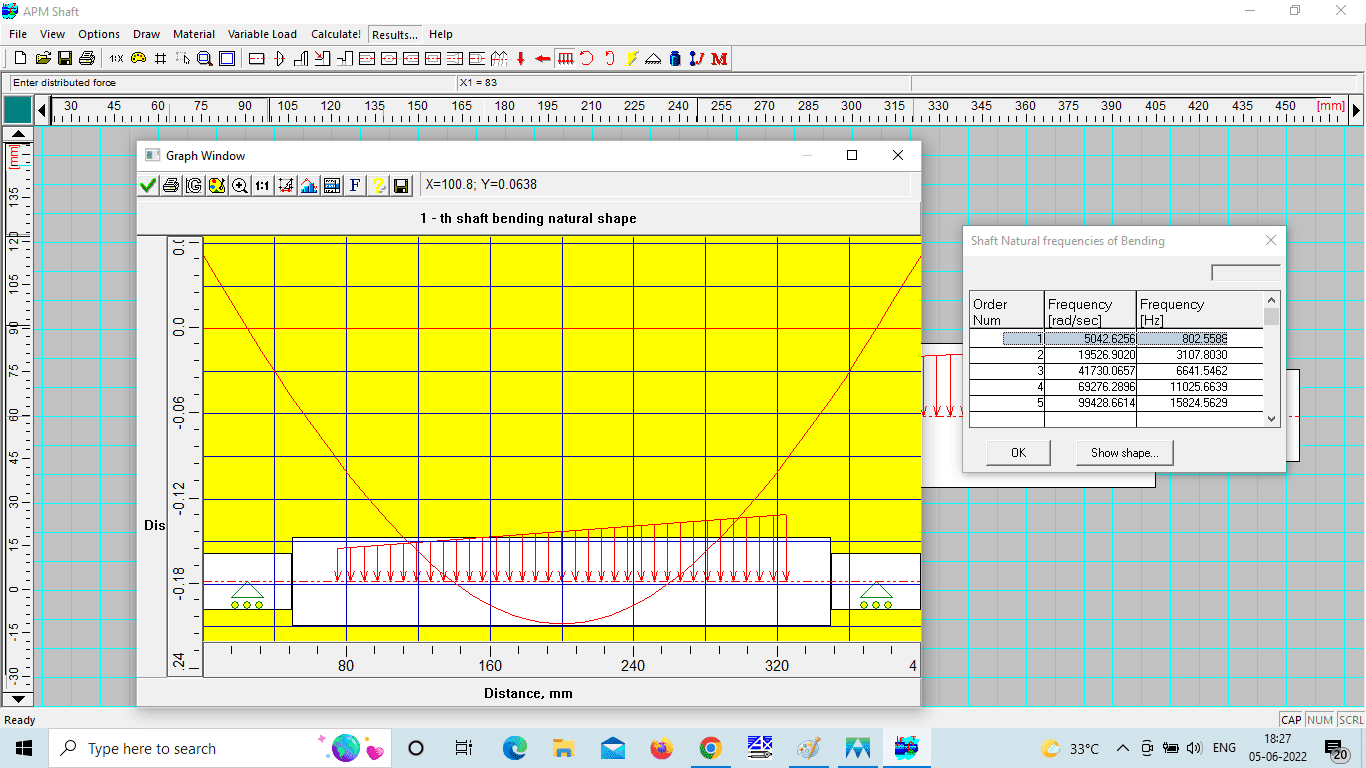
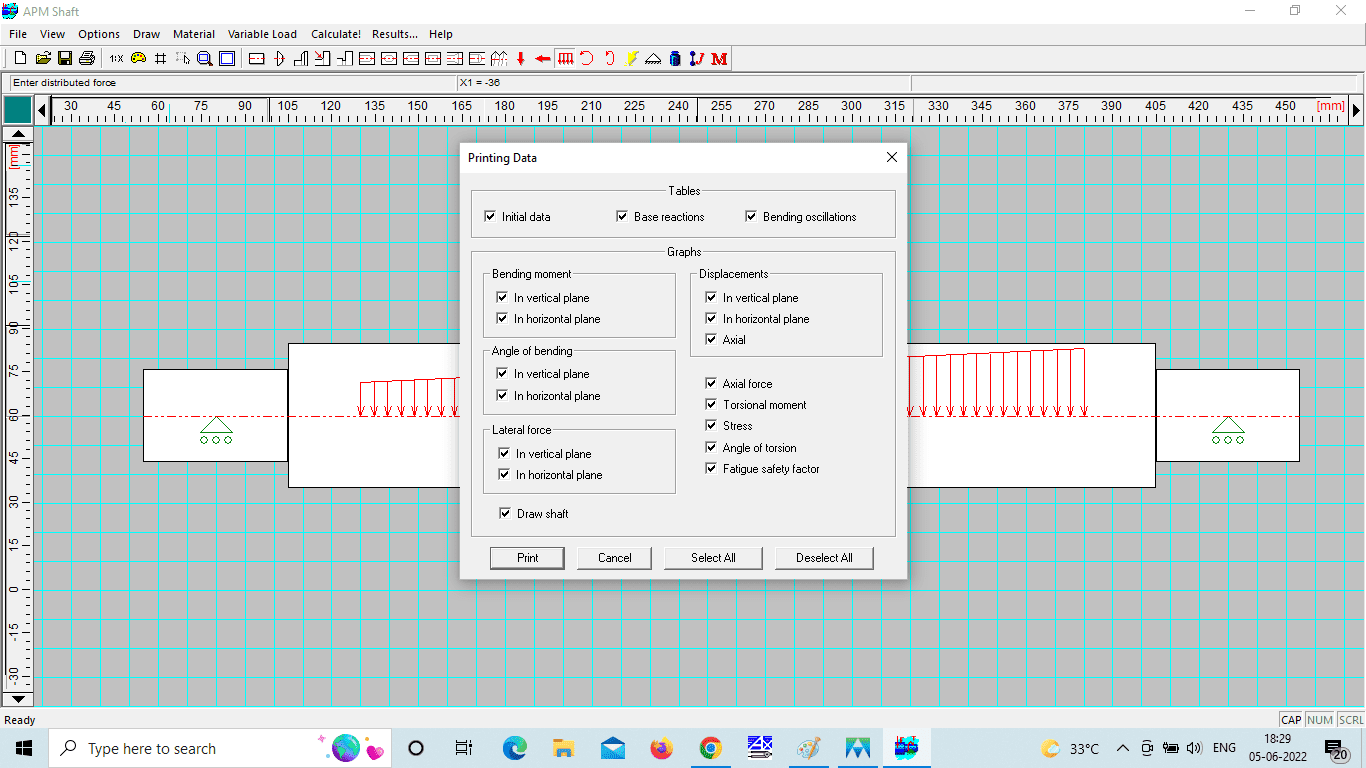
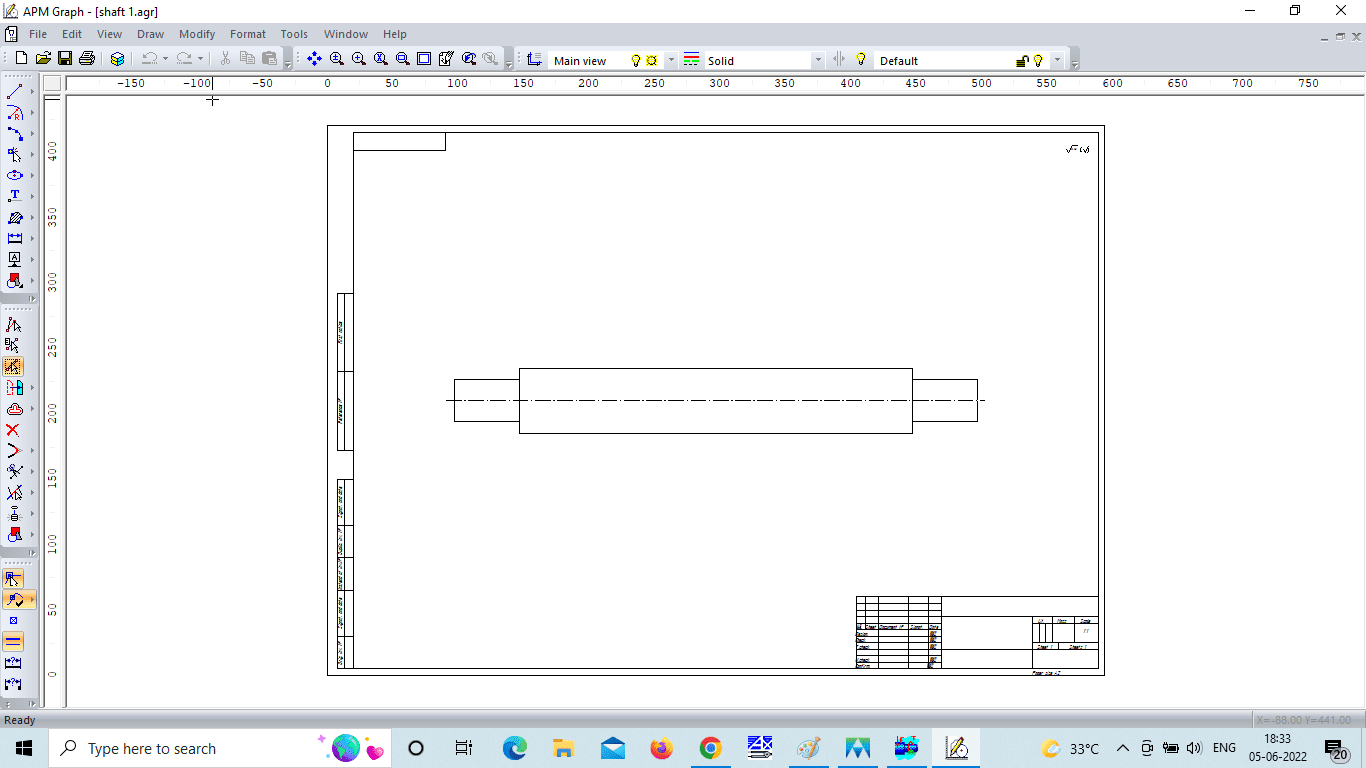
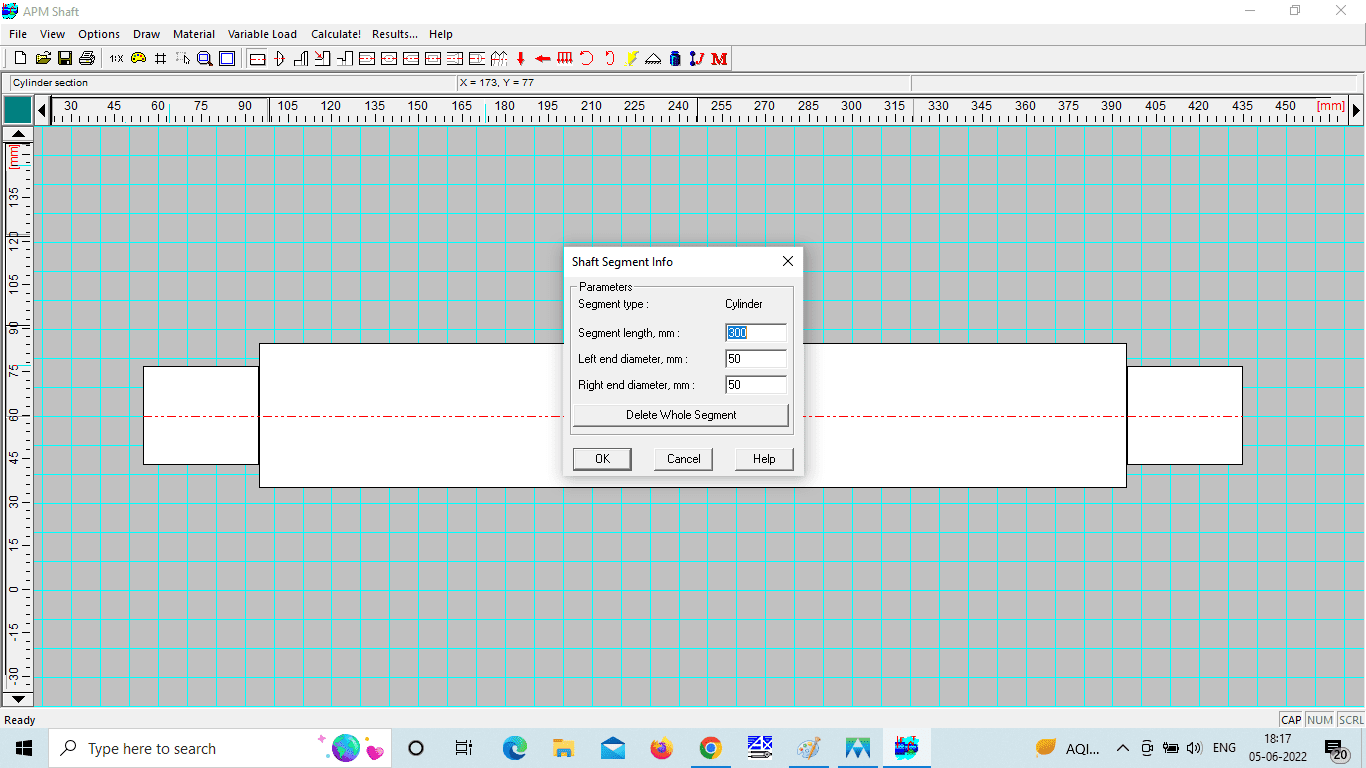
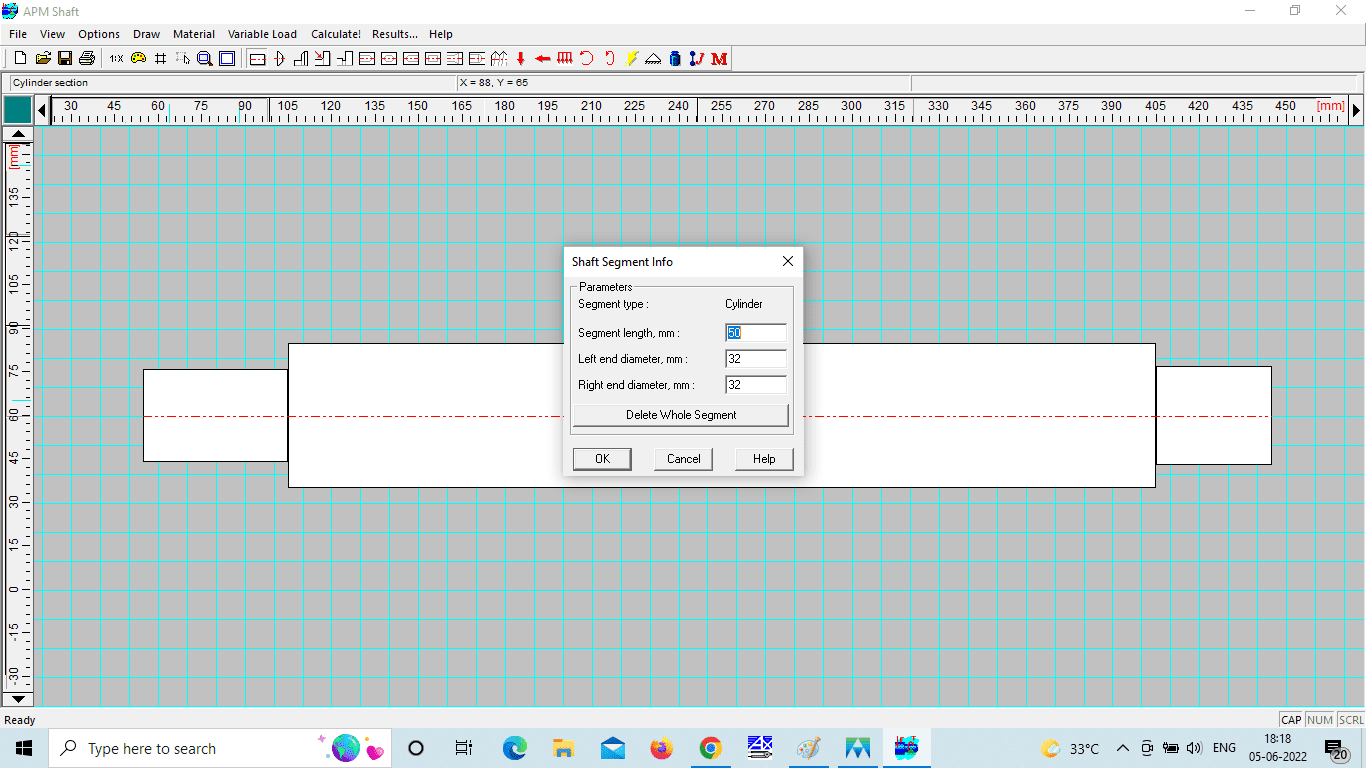
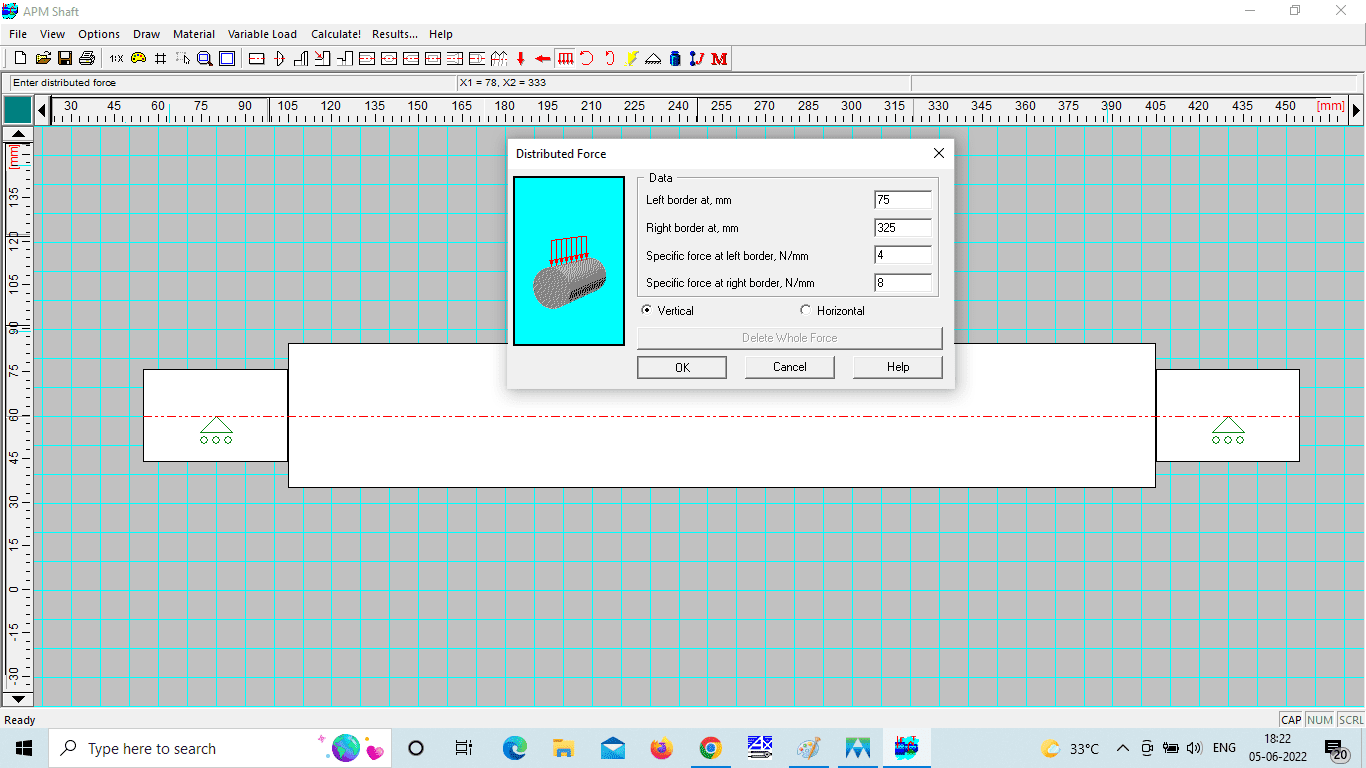
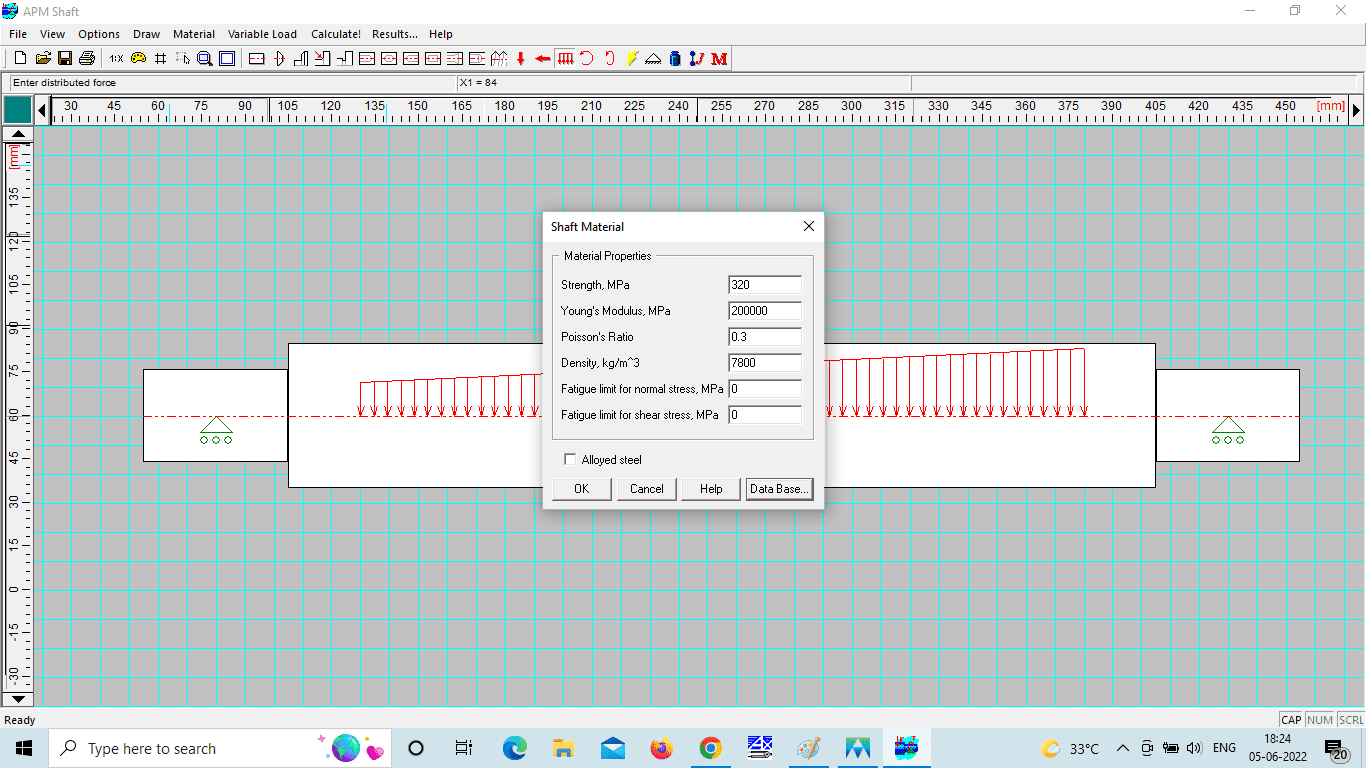
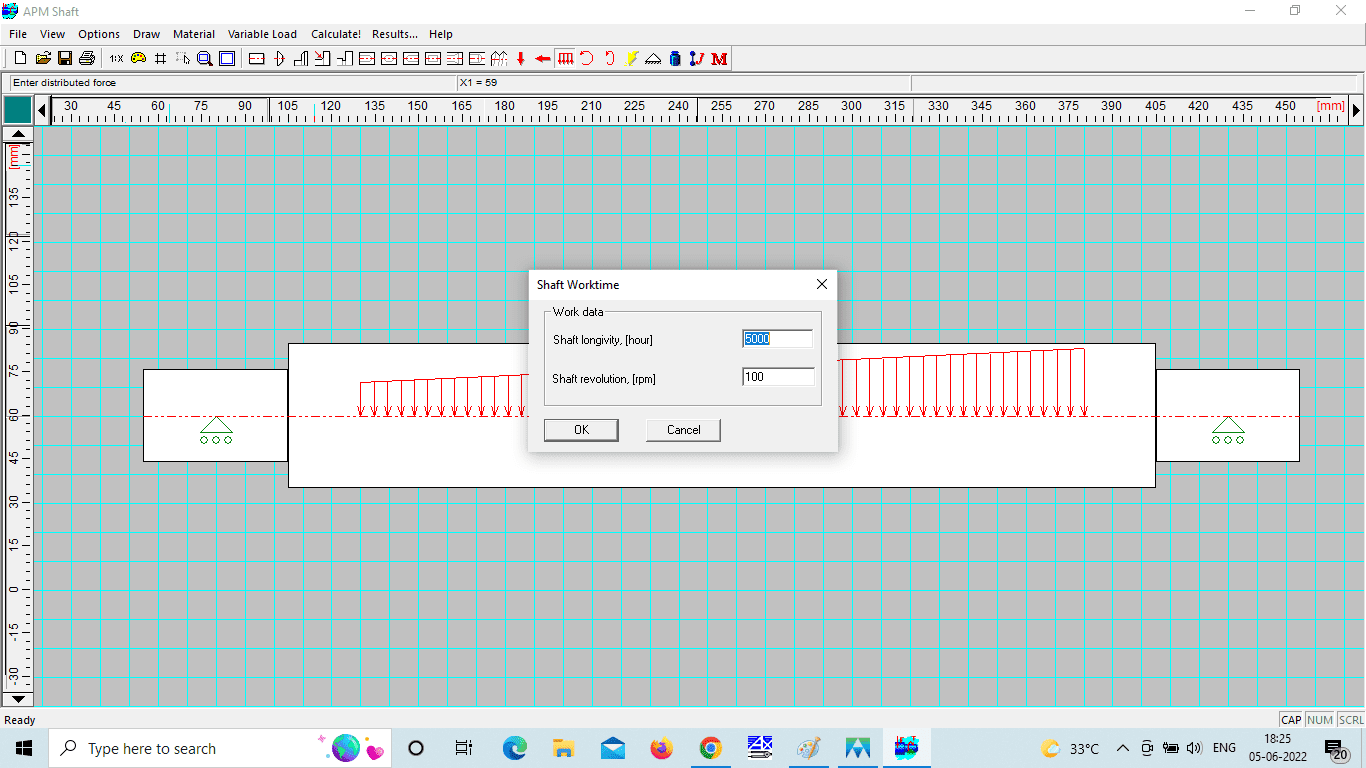
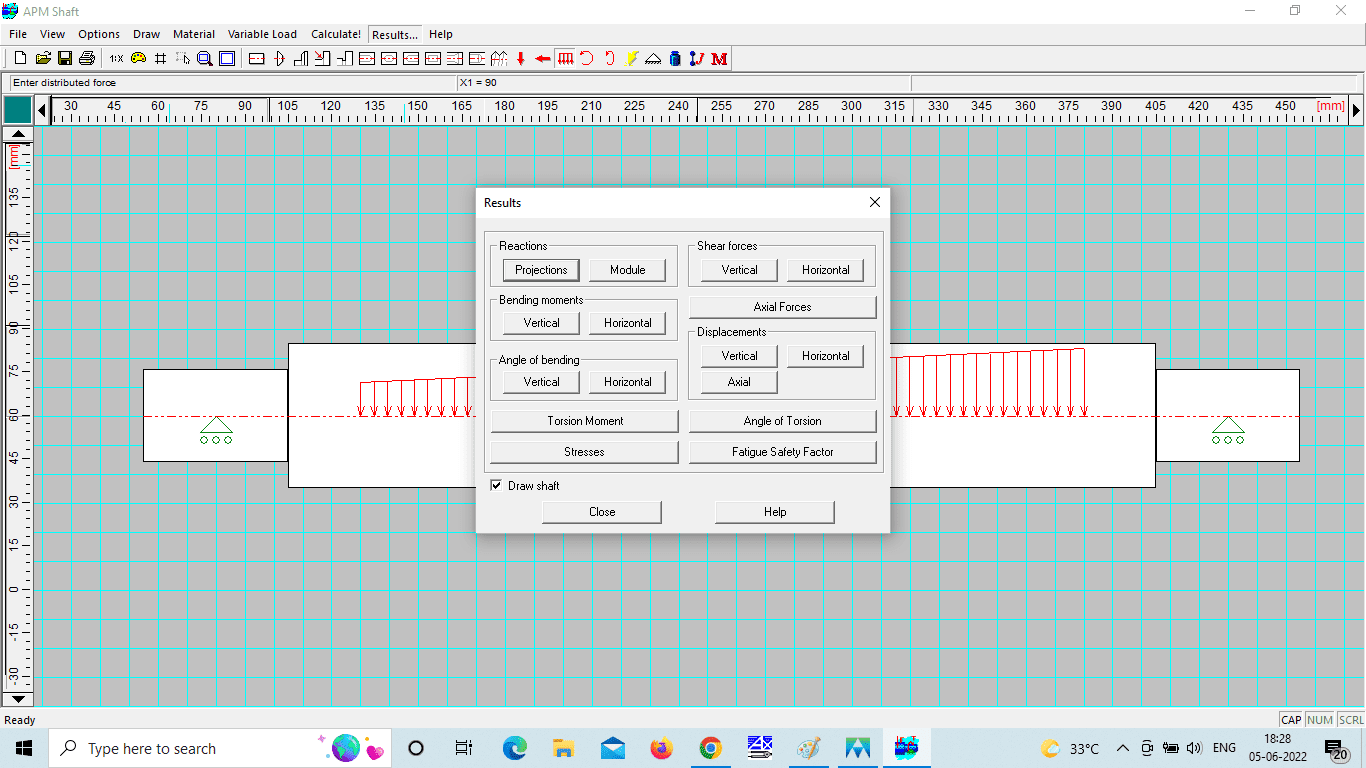
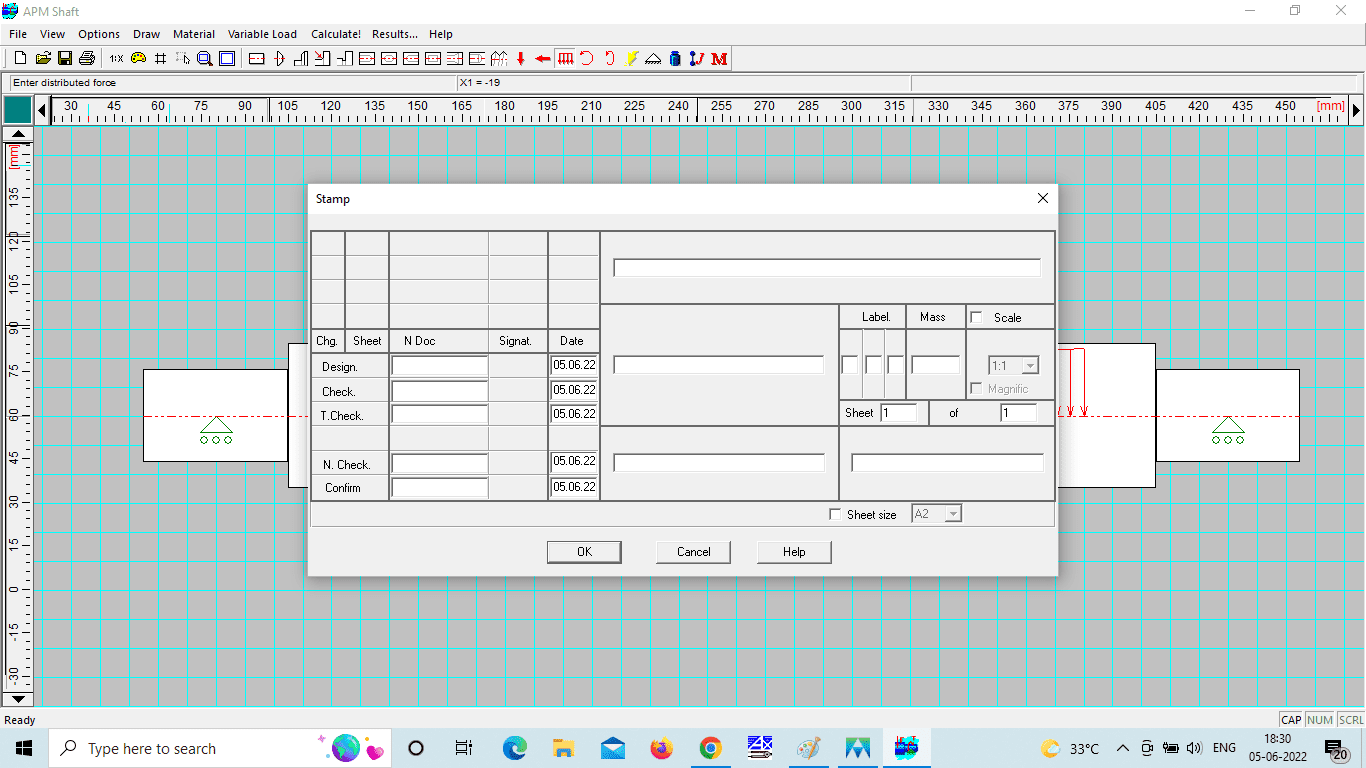
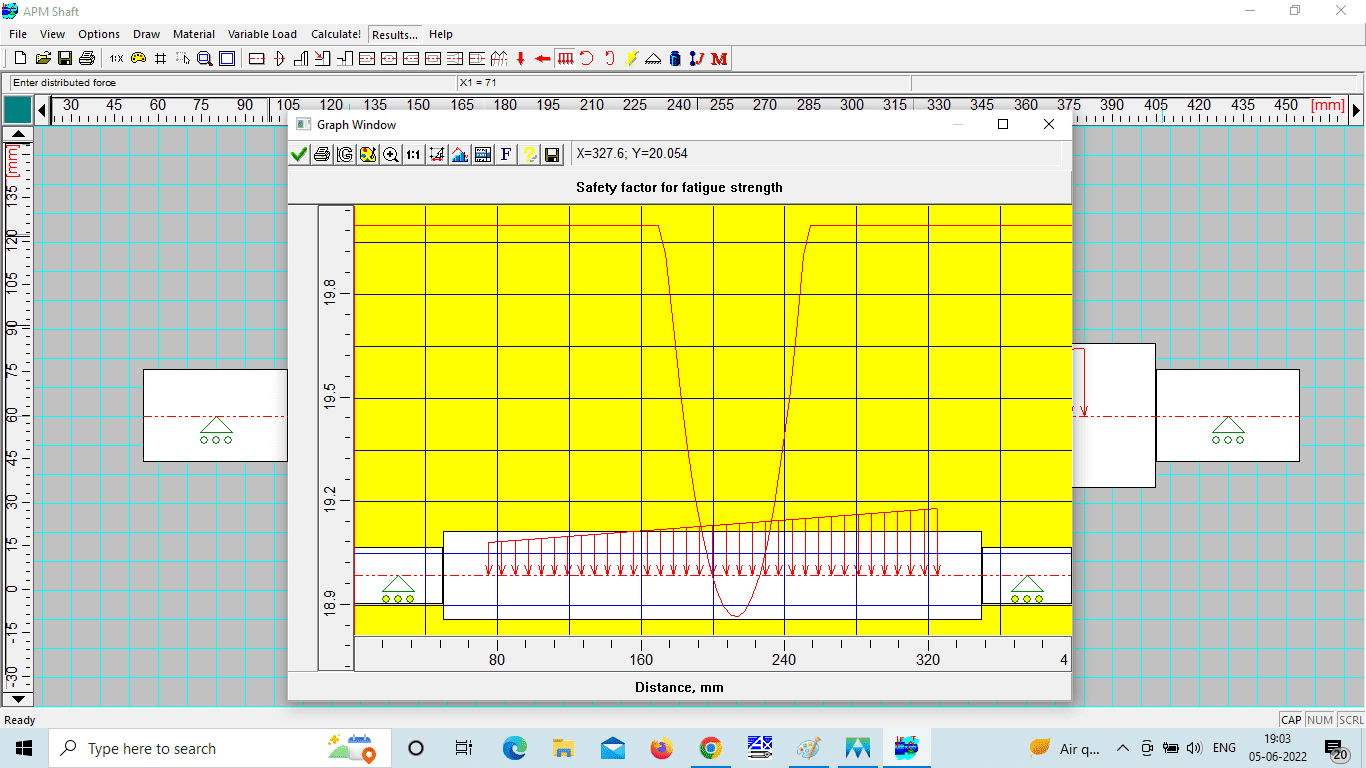